Organic photovoltaic films: polymers shine (brightly)
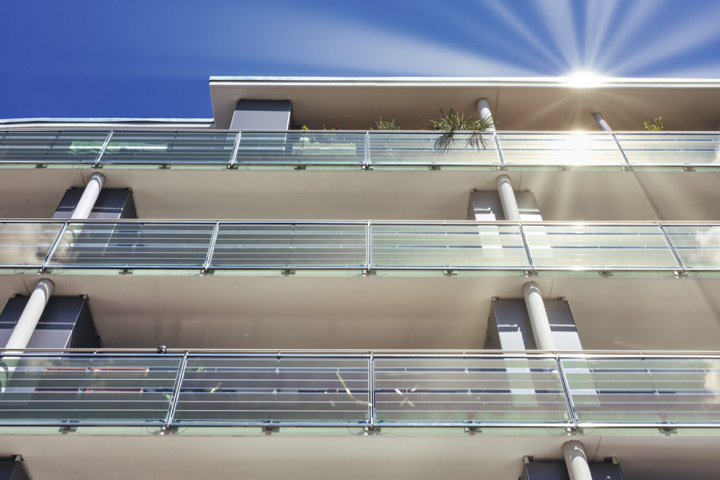
ASCA is the global leader in organic photovoltaics (OPV). Can you tell us what OPVs are?
Unlike traditional solar panels made of silicon, OPVs are made from organic, carbon-based molecules. More specifically, these are semi-conducting polymers which release electrons when stimulated by sunlight, and these electrons generate electricity as they move. That’s a simplified explanation, but that’s more or less what’s happening.
![]() |
What’s the benefit of using this technology?
There are a lot of benefits! Firstly, ASCA® films are transparent and can be produced in a range of colours. They’re also flexible and can take on a variety of shapes, making them perfect for both concave and convex structures. In addition, they can be applied to a wide variety of materials, from metals and concrete to glass and textiles, and their “roll-to-roll” manufacturing process requires little energy (a temperature of 100 °C is all they need, compared to the 1,000 °C required for silicon panels) and doesn’t call for scarce materials. Finally, they’re lightweight, so existing structures don’t need to be reinforced prior to their application, meaning these films can be installed anywhere.
![]() |
Could you tell us more about the “roll-to-roll” process?
We apply several layers of our semi-conducting polymer in liquid form to a polyethylene terephthalate (PET) film. One of these layers acts as the cathode, another as the anode. We use different photoactive polymers for this, but I won’t say any more than that. Even though we have dozens of patents protecting our process, we still want to keep a few things secret. The five layers that make up the film are coated continuously at high speed in a process known as “roll-to-roll”. A laser then breaks down the material, enabling the cells to be connected together. The whole assembly is then encapsulated in a barrier film to ensure the module is completely watertight. After that, all that’s left to do is install it and connect it to the electrical system of the building or object it’s installed on. With this technology, we can produce around 1 million m² of photovoltaic film every year.
![]() |
The competition in your field is fierce. What makes you stand out?
Competition certainly is fierce. But before I talk about what makes us stand out, I’d like to say that OPV technology is something China, the global leader in the traditional photovoltaic panel sector, has yet to master.
![]() |
We’re proud to be contributing to our country’s industrial autonomy and, indeed, that of Europe.
Our modules are all produced in France and Germany, and we’re also fully in line with the United Nations’s Sustainable Development Goal 13, which calls for urgent action to combat climate change and its effects. |
Going back to our strengths, I’d say that we’re one of the only companies that offer a film that can be applied to all types of surfaces, no matter their design.
However, we have no intention of slowing down, and we’re still very active in the field of research, including core research, in a bid to constantly improve our materials and find the most optimal combination. |
![]() |
Selecting the right polymers is crucial to achieving the best possible performance because their ability to absorb light might differ according to their intrinsic properties. The specific qualities of the selected material influence the composition of the active layer, which can change from one generation to the next.
We keep a close eye on new developments in the plastics field, and we’ve forged strong links with numerous partners to obtain the most efficient polymers for our roll-to-roll production process. In 2020, we were achieving over 25% efficiency in a low-light environment. We owe this great score to the recent integration of materials developed with our partner Raynergy Tek, a Taiwanese chemical company specialising in organic semiconductor materials for OPVs. Since then, we’ve achieved a further 40% increase in efficiency by integrating new polymers, known as non-fullerene acceptors (NFAs). These were also developed with Raynergy Tek.
We also know that aesthetic appeal often plays a vital role in a product’s success. To appeal to designers and architects, our modules need to be available in a range of colours. Today, we’re one of the few companies that offer customers a fairly extensive range of colours.
![]() |
Can you tell us a bit about what you’ve been involved in?
Of course. I’ll start with a project that’s garnered a lot of attention, and with good reason — the Novartis pavilion, which has recently been opened in Basel, Switzerland. The architects’ idea was to create a building with a media façade that was self-sufficient and powered solely by the sun.
![]() |
The building’s shape is complex, a little bit like a truncated sphere. It wasn’t possible to integrate traditional solar panels into the design without losing the formal purity of the building, which is why the architects turned to us. |
The OPV modules are designed to follow the structure’s curves and are integrated directly into the media façade, supplying it with energy using only sunlight. The 30,240 LEDs that make up the façade are then used to broadcast animations. Thanks to our organic solar cells, the pavilion comes to life every evening for around thirty minutes. We’re also proud of the glass balustrades we integrated our cells into, even if they’re less spectacular, at least in visual terms. To make this a reality, we worked hand in hand with a German glassmaker. These balustrades can be found in buildings in Möhringen, near Stuttgart, and a total of 88 glass panels have been installed. The electricity produced by the solar cells can either be fed into the public grid or consumed directly. The combination of the OPV balustrades and the photovoltaic panels installed on the roof means the building meets the “passive” housing criteria in terms of energy performance. The technology used here is similar to what we used for a solar greenhouse in Ireland. This greenhouse incorporates 15 triangular solar modules laminated between two polycarbonate panels that recharge a battery during the day. At night, the battery powers a UV lamp for 3 hours, extending the plants’ growth period by the same amount.
I would also like to mention the street furniture, such as solar trees, that’s also been installed in Germany. These 6-metre-high solar trees supply energy to an electric bicycle station in a retirement home in Löchgau. The “leaves” of each solar tree consist of nine green OPV modules, each 2.5 m long and laminated between two polycarbonate panels with the help of a glassmaker.
![]() |
Can they also be incorporated into textiles?
Absolutely, mainly in ethylene tetrafluoroethylene (ETFE), which is used in many large-scale structures. The fashion world is also interested in our films, for example, Art by Physicist, an American start-up specialising in sustainable high-tech fashion. This group has created a smart jacket and dress that can recharge electronic devices while you’re on the move, thanks to our panels, which have been integrated into the fabric in the shape of a lotus. The options are endless; my mind is already travelling to smart backpacks that can recharge phones. All that’s left is for designers to unleash their creativity!
![]() |
This interview was conducted in June 2023. At the time of this article’s publication, the ARMOR GROUP, a player in the solar energy sector through its subsidiary ASCA, has announced that it’s refocusing on producing organic photovoltaic film (OPV) for solar solution designers. This will allow the company to concentrate on its longstanding expertise in manufacturing ink and coatings for semi-finished industrial products while ceasing to design and develop solar solutions and architectural projects, its downstream activities.