Biosourced plastics are one of the solutions for decarbonising our industry
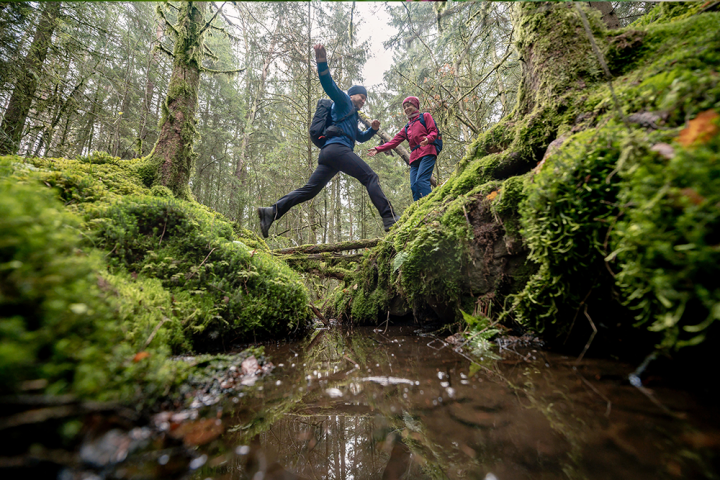
As Senior Innovation Manager, what is your role at Vaude?
We are looking to have a completely neutral impact on the environment and we know that this means decarbonising our products and our industry in general. Our goal is very concrete as we estimate that by 2024, 90% of our production will contain more than 50% recycled or biosourced materials. That's the goal for the future and we are working hard to achieve it. My role is both scientific and technical, as I am in charge of evaluating new materials, mainly textiles, that will help us to achieve this goal. Biosourced materials are very high on the list of priorities.
![]() |
What is your opinion of biosourced materials?
What are we talking about, exactly? In our business, we can use biosourced materials that are not chemically processed and are therefore entirely natural, such as organic cotton, hemp or kapok. Animal-based raw materials such as down, merino wool or leather can also be used. Then there are bioplastics, polymers chemically designed from renewable materials such as wood fibre, castor oil, sugar cane, etc. They are an interesting alternative to petroleum-based polymers because they help to decarbonise our industry.
But I think we need to go even further, because a product or material having an “organic” origin does not necessarily mean that is sustainable. We need to analyse its life cycle by looking at its origin: how it is produced, how much water it requires, whether it requires pesticides, etc., and its management at the end of its life: is it compostable? Can it be recycled?
In your opinion, are bioplastics preferable to recycled plastics?
I think that recycled plastics will become extremely commonplace, but they won't be able to do everything. Not only because they are not infinitely recyclable because they lose some of their properties over the course of the different cycles, but above all because they will not be produced in sufficient quantities to meet the ever-increasing demand for polymers worldwide. It will always be necessary to produce virgin materials. To make them more neutral, substitutes must be found to free us from oil and gas. This is where biosourced polymers come in. To answer your question frankly, it is not wise to compare recycled plastics with biosourced plastics. They are complementary!
![]() |
Which biosourced polymers do you use and what are their applications?
There are several. Some are very well known, others less so, such as s.Café®. The latter is a polymer based on coffee grounds from which an oil and subsequently a polyol, a chemical element that is essential for making polyurethane, are extracted. Thanks to this innovative technology, we can replace up to 25% of conventional polyurethane with s.Café®.
![]() |
This biosourced material, like recycled PET, is used in our waterproof and breathable Ceplex Green membranes.
They are used to make our mountain jackets windproof and rainproof. We are particularly pleased with the result because these membranes are very effective. |
Polyamides are used in a large number of our products. We have tested almost all types of biosourced polyamides available on the market and found that polyamide 6.10 has interesting properties and can be used as a conventional polyamide as it performs well. It is a castor oil-based polyamide produced by Evonik and called Vestamid Terra HS (PA 6.10). We were the first to use it. Ricinus (castor bean plant) is a perfect plant because it is truly 'sustainable': it does not require chemical resources or artificial irrigation to grow. It is grown in dry areas that are not suitable for other types of agriculture. It is a very popular food for caterpillars but not edible for humans and other mammals. It is therefore not a food crop. We have been using polyamide 6.10 since 2018 and, in order to incorporate it in satisfactory quantities, we had to rethink our entire supply chain organisation. It was a lot of work, but many lessons were learned and we can now produce a large quantity of garments using this biosourced polyamide. This is another step towards our 2024 targets.
We also use Covestro's biosourced thermoplastic polyurethane (TPU) for our hiking boots, especially for the midsole. The midsole is placed at the front and rear of the shoe. At the front, it absorbs shocks from rocks and pebbles and at the back, it contributes to the stability of the shoe, which must be neither too soft nor too rigid. This sole is a mixture of biosourced EVA (most often based on sugar cane) and biosourced TPU. |
![]() |
Finding the latter was a real challenge because our specifications prohibit the use of genetically-modified agricultural materials (GMOs). However, 1,3-propanediol, one of the chemical components of TPU, can be extracted from palm oil, which is very often produced from genetically-modified plants. We didn't want to take any chances and after a long search we finally found a supplier who could produce propanediol from used cooking oil. The supplier is Metabolic Explorer, a French start-up that now supplies this molecule to Covestro to make its bioTPU. Again, the end result is as good as we expected.
![]() |
Biosourced plastics are sometimes criticised because they can be derived from food resources. Are you vigilant on this point?
This is a very broad issue that I think is less and less debated because there is a consensus that if we want to ensure food security for the whole world, we must not convert food crop land into crop land for biofuels and bioplastics. As far as bioplastics are concerned, very little agricultural land is devoted to them. That said, they do exist, but as the Nova-Institute, an independent research institute working on the transition of the chemical materials industry to renewable carbon, so aptly puts it: there is no such thing as an ideal material! All raw materials have advantages and disadvantages.
Coming back to bioplastics, I think that their "cultivation" should be done without deforestation and avoiding land-use changes. I am often surprised by the reactions of the general public and even of some politicians to these subjects, which are not all well understood. Discussions are hardly constructive because they are based on emotion. I imagine it would be interesting to better inform these populations with objective data.
![]() |
Indeed. To find out more about biosourced plastics, see our article Did you say "Bio-Based"?. To find out more about Vaude's environmental policy: VAUDE CSR-Report – Integrated Sustainability Strategy